P84 filter Cloth
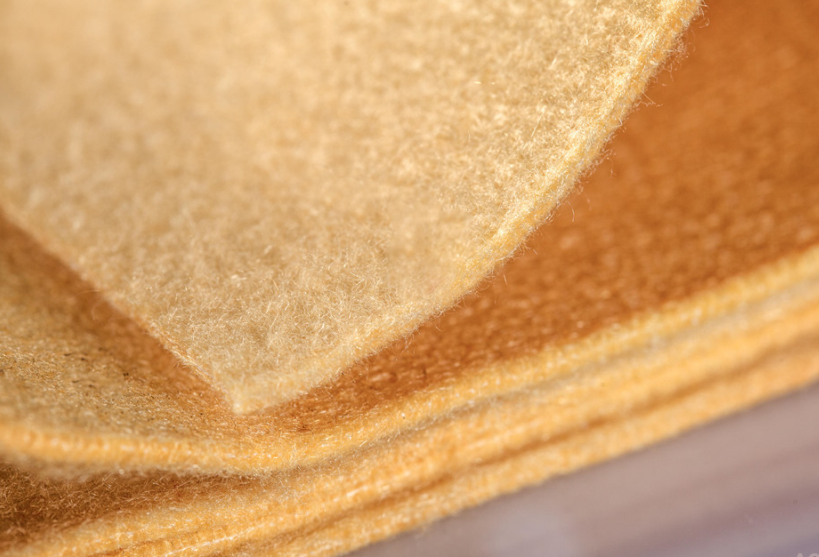
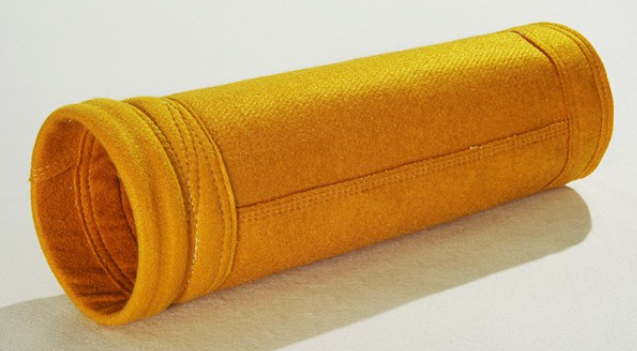
P84 punched felt is a high temperature filtration media used in pulse jet baghouse dust collectors. This material performs well in dry, high heat applications. It is strong, abrasion resistant and good for applications up to 460° F.
It is one of the most common materials used to make filter bags. And has high temperature resistance, good corrosion resistance and acid resistance. P84 needle felt provides a unique and cost-effective solution for many demanding industrial baghouse applications. It is used in a wide range of applications such as mineral processing, low-acid coal-fired boilers, asphalt/hot mix plants, soil remediation facilities, and more
Parameters
Product Name | 100% P84 fiber Filterbag | |
Product Code | AASF-P84 | |
Physical properties | ||
Weave method | Needle felt | |
Thickness (mm) | 2.0 | |
Weight | g/m² | 500 |
Width | m | ≤2.20 |
Loss on heat shrinkage over 250°C (%) | 1.5 | |
Finish treatment | Singe, Calendering, Heat setting | |
Air Permeability (L/m²S@200Pa) | 150-300 | |
Tensile Elongation | Warp | < 20 |
Weft | <40 | |
Tensile Strength (N/50mm) | Warp | ≥800 |
Weft | ≥1000 | |
Temperature | ||
Continuous temperature | °C | 260 |
Instant temperature | °C | 280 |
Used in high temperature resistance working condition |
Asphalt – Durable construction required for abrasive, high temp environments. Hotmix or batch plants, whether natural gas, waste oil, fuel oil, etc. Replacements filters for OEMs like Astec, Gencor, Standard-Havens, etc.
Cement – Filters for all areas of plant: kilns baghouses, silo bin vents, nuisance dust collection, etc. Our filters exceed all EPA emissions standards (NESHAP, CMAT, MACT for portland cement, PM2.5, etc.). Replacement filters to fit ABB/Flakt, Flexkleen, FLS/Fuller, Mikropul, Norblo, Redecam, Solios and other dust collector OEMs.
Chemical – Filter fabrics for acidic or alkali compounds, corrosive or abrasive elements, etc. (lime, calc, fertilizer, plastics, etc.) – Special treatments and fabrics available. We can advise on the best combination for performance and cost.
Food Processing – FDA approved food-grade fabrics construction available for dust collectors used in food production, transportation and packaging such as dust collectors on milling equipment, blenders, mixers, granulators, grain elevators, storage silos and more.
Foundry and Metal Products – Filters for units used on arc/induction furnaces, casting operations, and precious metal reclamation. Fabrics and coatings for use in high temperature environments with need for high efficiency fume and smoke collection. Filters to fit major OEMs like Amerex, Norblo, Wheelabrator, and others.
Power Generation and Industrial Boilers – Our filters exceed new EPA emissions regulations for boilers and power generation (Mercury and Air Toxics, Boiler MACT, NESHAPs, etc.). We have much experience working with biomass and coal power production facilities to overcome technical challenges to meet new EPA regulations. Filter fabrics and treatments include PPS, P84, PTFE/Teflon (fabric), fiberglass, and ePTFE membrane.
Wood, Sand and Minerals – Often requires filters with flame resistant coatings, or constructed from nonflammable materials. We can manufacture filters to fit collectors from MAC, Murphy-Rodgers, Pneumafil, Torit, Farr and others.
Unique Applications
For relatively low to medium temperature operations (Up to 300°F normal operating, 350°F surges), many collectors perform the best using filters made from polyester, and polypropylene felts. In many applications that have heavy dust loads but require high efficiencies such as cement production, or power generation (coal-fired, etc..), the use of fabric laminated with ePTFE membrane is the best option.
For higher temperature processes, (400°F normal operating temp, 450°F surges or higher), high temperature fabrics such as Conex™/Nomex™ felts (Aramid fabrics) and P84™ polyimide felt can be employed.
Selecting the Correct Baghouse Filter is Vital for Obtaining Optimum Performance from your Baghouse
The most important part of any baghouse is the filters themselves. Selecting the wrong type of filter will result in the system performing inefficiently, emitting excess pollutants and damage to other system and plant components. However, the correct filter will maximize performance, increase filter life and reduce system downtime and thus save you money. That is why it is vital to select the correct filters for your baghouse, and see that they are installed correctly.
Certain applications require dust collector filters with special properties. Filters used in food processing may need to have a food grade rating in order to meet safety regulations. Other processes necessitate the use of antistatic fabrics and coatings such as epitropic felt with antistatic coating. Others need to be acidic or alkali resistant such as homopolymer acrylic felt.