In modern industrial dust removal systems, electromagnetic pulse valves serve as the “heart components” of pulse bag filters. Their performance directly impacts equipment efficiency and service life. As intelligent switches for compressed air, these valves precisely control filter bag cleaning cycles through commands from pulse controllers, ensuring stable system resistance and optimal operation.
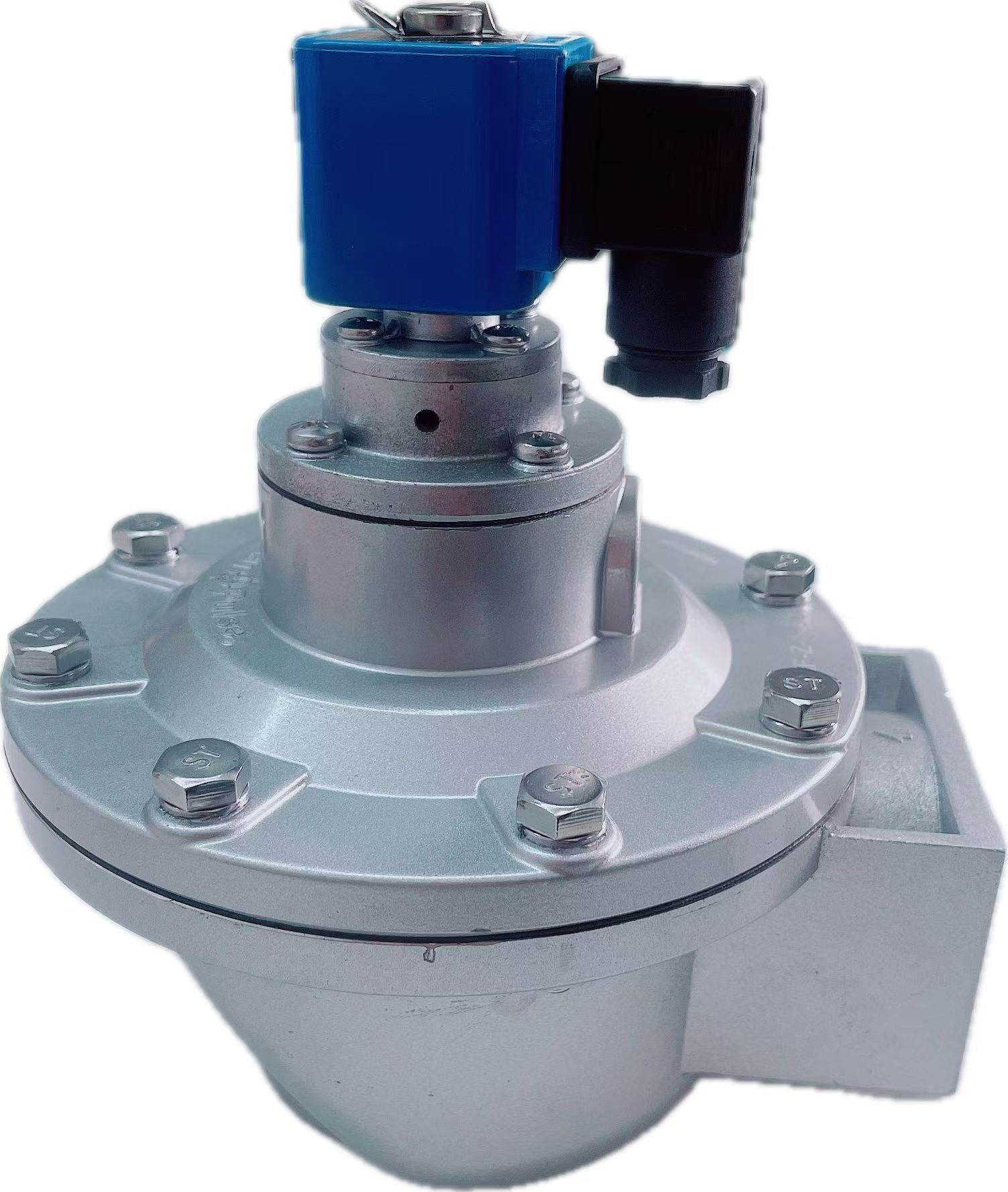
The working principle relies on differential pressure control: when energized, the electromagnetic force moves the spool to open the pressure relief port. This rapidly drops the pressure in the rear chamber, lifting the diaphragm via compressed air for instantaneous jetting. After power-off, the spring resets the spool to close the port, restoring rear chamber pressure and reclosing the diaphragm. This process demands precise diaphragm design and airflow engineering to achieve sub-100ms response times and stable jetting pressure.
Typical technical specifications include aluminum alloy bodies for -10°C to 55°C environments, 0.4-0.7MPa operating pressure, and compatibility with AC220V/DC24V power supplies. The diaphragm must resist wear and corrosion, with high-quality models offering over 1 million jetting cycles.
Selection criteria depend on dust collector size, air source conditions, and cleaning frequency. Right-angle valves (90° inlet/outlet) suit small-to-medium systems with vertical installations, while submerged valves (integrated into air tanks) provide lower resistance and higher efficiency for fluctuating air pressure scenarios.